Researchers from the Fraunhofer Institute for Laser Technology ILT haveteamed up with project partners to develop an AI module to help with lasermaterial deposition. This technique is used to repair worn bucket teeth andother tools used in mining.
Tools used in mining are exposed to tremendous wear. Excavator bucketswith worn teeth or dull chisels and rock crushers are typically melted down andreplaced with new ones. But, that is expensive and resource-inefficient.
Laser material deposition (LMD), also known as cladding, presents analternative to this. In this method, a metallic powder and the laser beam areguided through an optical system in such a way that the laser beam creates alocalized weld pool on the component, where the powder is deposited. The systemmoves over the tool, depositing high-quality metal alloys, path by path andlayer by layer. This restores the original contour of parts such as a wornexcavator tooth or drill bit exactly as they were before.
In the Artificial Intelligence Enhancement of Process Sensing for AdaptiveLaser Additive Manufacturing (AI-SLAM) project, Fraunhofer researchers arecombining laser technology with artificial intelligence. “The goal of theproject was to automate all the steps, from mapping the defects to planning thepaths and parameters to be used during welding and, then, to the actualexecution and quality control,” explains Max Zimmermann, the project managerresponsible for LMD coating and heat treatment at the Laser Material Depositiondepartment at Fraunhofer ILT.
Project partners are the National Research Council of Canada, McGillUniversity, and companies including Calgary-based AI firm Braintoy, and ApolloMachine and Welding, which is based in Edmonton. BCT, a software developmentcompany based in Dortmund, is also involved.
Ultra-hard tungsten carbide andstainless steel
During the repair process, the laser optical system follows apre-calculated path over the surface of the tool. Stainless steel is smelted atapproximately 1300°C and deposited, while nozzles simultaneously aim jets oftungsten carbide particles at the same area. The particles combine with themolten steel to form an ultra-hard coating on the tool after cooling,protecting it against both wear and corrosion.
One of the challenges for the team of researchers was to find the optimumratio of tungsten carbide particles to steel. “Too high a proportion ofparticles makes the coating brittle and prone to cracking, but with too muchstainless steel, it’s too soft, so it wears down quickly,” Zimmermann explains.
The laser power also has to be calibrated so the temperature is highenough to melt steel but not so high that the tungsten carbide particles meltas well (at approximately 2900°C). If that were allowed to happen, the tungstencarbide would become too soft.
There are many other parameters besides: the distance between the nozzlesand the surface, the speed at which the system traces its path, overlap betweenpaths, the power of the laser, and much more. In all, there are 150 parametersto set and coordinate when planning a single repair process.
AI plans and controls repairs
For the AI-SLAM project, the Fraunhofer researchers developed aseveral-part AI module that governs this complex planning and control process. Asthe first step, a line laser uses a CMOS camera to capture the worn contours ofthe tool, such as an excavator tooth.
This produces an image of the current surface geometry. The image iscompared against the contour of the tooth when new, which is also stored in thesoftware.
Finally, the module uses the difference to calculate the path andthickness of the metal coating that should be applied. A camera feeds images tothe AI during the coating process so it can detect any discrepancies or errorswhile the work is under way.
Much faster and less error-prone
Project partner BCT incorporated the researchers’ AI module into itsOpenARMS operating software, which translates the parameters recommended by theAI for the welding process into control commands. This means human operators nolonger need to type in the machine codes, a time-consuming and error-pronestep.
Calgary-based Braintoy is responsible for the machine learning algorithms.It also provides the plat-form for data analysis in the LMD system.
All of the solutions work together, so the repair process takes placeautomatically and without errors. “All the human operator needs to do is pushthe start button,” Zimmermann says.
To be able to deposit the metal coating on the tools’ complex surfacegeometry from a consistent distance, the laser head moves on three axes andalso features two axes of rotation.
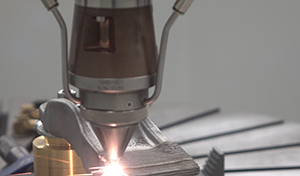
© Fraunhofer ILT.
Mining tools like this excavator bucket tooth are subject to extreme wear.Ultra-accurate AI-assisted laser material deposition is used to perform repairsquickly and cost-effectively right on the machine.
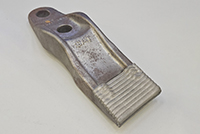
© Fraunhofer ILT